Essential Energy is using drone-captured imagery and software to create “intelligent” three-dimensional models of its substations that engineers can interact with and plan upgrade works remotely.
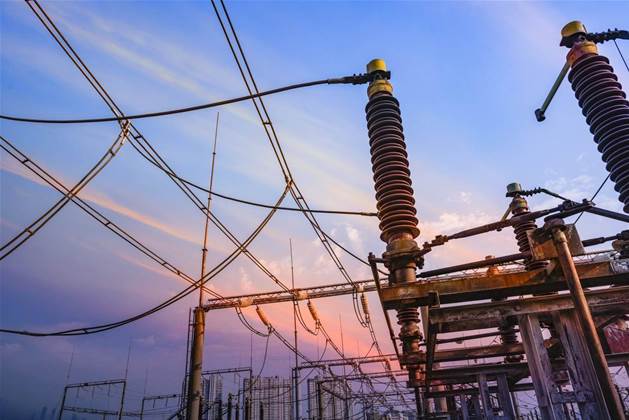
In this week’s episode of the iTnews Podcast, substation design manager Jason Streatfeild discusses the work of his team of engineers and drawing officers that manage all aspects of design for nearly 400 substations across the state, and the growing influence of technology on this function.
Essential Energy is a NSW government-owned electricity distributor covering 95 percent of the state as well as some parts of Southern Queensland.
Its infrastructure - including the nearly 400 substations - is used in the supply of electricity to more than 840,000 customers.
In major parts of the state, there may be one substation per suburb; in smaller towns, it is often one per town.
Much of Streatfeild’s team’s work involves upgrades to existing substations, although there are some newer builds occurring, mostly adjacent to renewable electricity generation sources.
“A lot of the network in NSW was built quite a few years ago and a lot of the infrastructure is ageing, so we're doing a lot of work, especially in our regional-remote areas, replacing lots of different equipment in existing sites,” he said.
“We very rarely in the last few years have been building any greenfield [substation] sites, but a lot of those are probably coming along in the last 12 months with our increased solar connections and wind farms.”
Streatfeild said that one of his team’s biggest challenges traditionally was understanding what a substation looked like, in order to plan upgrade or maintenance works for it.
He said considerable site travel and effort over the past two decades had led to some improvements to drawing accuracy and records.
“We've done a lot of work at sites where we've upgraded the drawings or improved the [existing] drawing quality,” he said.
“A lot of the time, it would mean that we would need to go to site, take a lot of measurements, confirm what drawings that we had were accurate, and confirm that the construction was accurate to the original design.”
Newer drawings were then created using Bentley Systems’ MicroStation software and stored in a Bentley ProjectWise drawing management system.
Streatfeild said there are several reasons to want more accurate drawings of substations.
“The main one is safety: we need to ensure that we design our equipment to the right clearances so that we can ensure that when teams need to work on the equipment for maintenance and operation that they can do it with absolute safety,” he said.
Understanding exactly what is onsite can also prevent inefficient truck rolls, where a crew may turn up with incorrectly-sized parts due to inaccurate drawings or other information kept on file.
“Even for the smallest of jobs, if we're replacing equipment, and that equipment is on an existing site, it's mounted on a footing, it's on a structure, it's bolted down, it's got a particular connection point for cabling or for busbar,” Streatfeild said.
Bolts, for example, may be spaced differently at various sites.
“We need that sort of clarity on pretty much every job we do,” he said.
“We [have to] know what equipment we need [in advance]. We don't want to leave anything ‘up in the air’ for the construction teams to sort out onsite because we might guess the wrong size or have to provide alternatives for them.
“We want to get it right on the first go.”
Intelligent models
The next step in improving the quality and accuracy of substation drawings is to convert them from two-dimensional “lines, circles and text” to three-dimensional scale models that can be zoomed in with millimetre precision.
Essential Energy started on this path by adopting Bentley Substation and ContextCapture software to build three-dimensional models of its substations from drone imagery.
Streatfeild said ContextCapture, in particular, addressed “the area where we were most lacking in moving forward, which was having the ability to quickly and easily create a 3D model of our existing site.”
“In essence, ContextCapture was a ‘game changer’ in our brownfield designs. It allowed us to go and call up one of our drone pilots that are regionally based across the state, go and fly around a substation for somewhere between two hours and a day, take several thousand photos, send them back to my design team, and then we would internally process them using ContextCapture into a reality model,” he said.
“That reality model - to scale and in most cases, millimetre perfect - allowed us to answer every question we ever needed on that site.
“It also allowed us to import that into our Bentley Substation 3D design package as the basis of our design.
“We now knew exactly where all of the existing equipment was, and the detail on it was such that we could zoom in and read nameplates.
“This reduced our need for site visits to measure distances or take photos, or going back and asking again for another photo because we missed something.”
The substation models are also “intelligent”, in that a piece of equipment can be virtually removed from the model and a new piece added in, along with “all the connections and everything else that goes with it,” Streatfeild said.
“The output for us is fantastic because it's reducing our time for design. We know we've got all of the correct clearances and we've got all the other advantages of an intelligent system as well,” he said.
“It has lots of design engineering built into it. We can do lots of things from lightning protection calculations, which are done really at the click of a button instead of two or three days of an engineer poring over a calculator.
“It knows what equipment we put in our design so it automatically gives us a bill of material, even counting up all the nuts and bolts and washers.
“It counts up all of the lengths of conductors, and how many metres we use to join all of our equipment together.
“All those things are automatic. It just saves us so much time in checking and rechecking and making sure that we're doing the right things.”
Streatfeild said that date, Essential Energy has created “approximately 20 major projects using this system over the past 18 months, which is about $20 million worth of projects.”
He said more improvements to the system would occur over the next 12 months, including the purchase of new commercial-standard drones with higher-resolution cameras, which would improve the 3D models even further.
Subscribe to The iTnews Podcast at Apple Podcasts, Google Podcasts, Spotify, Amazon Podcasts or wherever else good podcasts are found. New episodes will be released every Monday.