Woodside Energy is piloting in production a cloud-based tool to provide real-time traceability of parts and materials ordered for maintenance work.
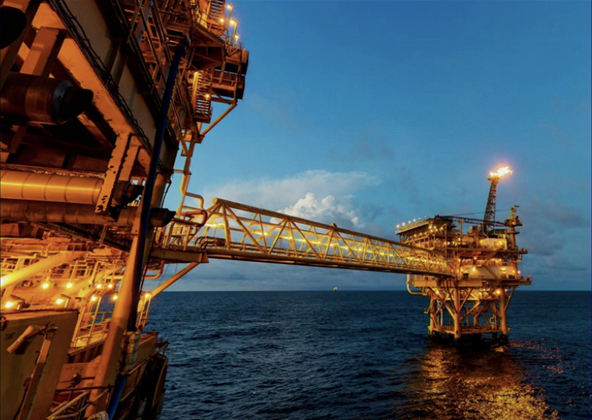
The tool has the internal codename of ‘Control Tower’ and is based on an “enhanced” version of Work Order Insights, a weeks-old module of the AWS Supply Chain application.
Woodside’s supply chain vice president Tracey Simpson told AWS re:Invent 2023 in Las Vegas last week that the next step will be to scale up the tool to run across the company’s global operations.
“This new capability has been delivered to a group of users as a pilot that’s currently live, so it’s being used in our operations,” Simpson said.
“The users include site-based staff who maintain our equipment, procurement professionals and logisticians.
“[Next], we’re going to explore scaling the product, actually to fit the size and global footprint of all of Woodside’s operations.”
Equipment maintenance work is managed and allocated internally via work orders, which “provide all the necessary information about a maintenance task and outlines the process for completing the work,” Simpson said. “[They] also detail the materials required to actually perform the job.”
However, she noted that it had been “historically … challenging” for maintenance teams to track down where the parts and materials they’ve ordered are at any one time.
That made it difficult to accurately understand whether the parts and materials would make it to site in time for the maintenance window.
It was, in fact, an additional layer of complexity: even just within Australia and its territorial waters, Woodside’s operations can be particularly remote, adding considerable time to supply chain movements.
In addition, parts and materials are “not easily substituted”, so understanding if a problem has arisen during the delivery of parts to a site as early as possible is important.
“We believed that we could unlock value by optimising stocking levels, streamlining business processes and minimising the need for rework or work deferral due to late parts,” Simpson said.
“Our teams told us that providing real time visibility and tracking and tracing of supply chain materials could positively impact our maintenance planning.
“Furthermore, we believe we can generate further efficiencies by delivering needed parts quicker, cheaper and more predictably.”
Simpson said a “roadmap” for creating real-time supply chain visibility was put in place and AWS ProServe - professional services - engaged “to help us deliver some of the solutions on our roadmap.”
She noted that enabled Woodside and AWS’ Supply Chain teams to connect and led to work to modify the already-new Work Order Insights service to suit Woodside’s needs.
Woodside had a lot of data already about parts and materials movements but wanted a way to make that source data more easily accessible, with different views of the data offered depending on the users’ role.
“Each of the groups [of users - maintenance, procurement and logistics] - has their own relevant view of the same dataset, which is really helpful when you know that everyone’s looking at the same thing,” Simpson said.
“This helps our teams very quickly identify the issues that are occurring either right now or have the potential to become a problem in the future, and it’s all done at the click of a button.
“They’re not trawling through multiple systems to try to get that information out and understand what they need to do.”
Users could apply a series of filters to data to understand where a parts delivery was deviating from schedule, so that action could be taken.
The filters enable users to drill down into the data, getting a simpler view of parts and materials that are “at-risk” of being delivered after maintenance work has begun, or that are simply “late”.
“Ideally, you want to be in an environment where there’s a limited number of materials running late, so one of the things our teams really like is the ‘at risk’ filter, as that actually gives you the opportunity to get in front of things and it helps you address issues that could become a problem if you don’t take action,” she said.
A delivery may not have been made because a purchase order wasn’t accepted by the vendor yet; or the vendor may be late, but Woodside’s teams can intervene to arrange a faster freight service to be used.
In addition to expanding the use of the tool, Simpson suggested that it could be augmented in future with some form of generative AI “to help our people make the best business decisions to return the highest possible value”.
“We also hope to use Work Order Insights to better integrate with our suppliers and help our business further optimise Woodside energy supply chain,” Simpson added.